[ad_1]
Hearken to this text |
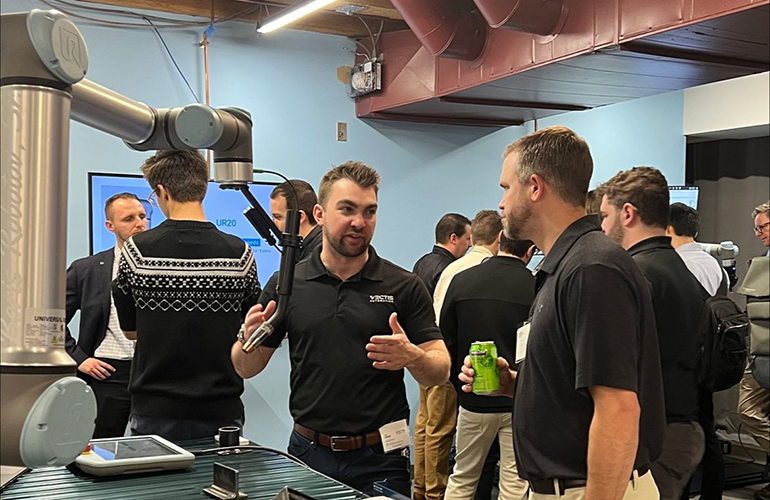
Common Robots companions mentioned and confirmed cobot functions at its Boston open home. Supply: Common Robots
BOSTON — As soon as dismissed as not succesful sufficient for industrial use, collaborative robots are simply starting to assist producers and provide chains. At an open home at its U.S. headquarters yesterday, Common Robots A/S confirmed about 400 attendees that cobots are prepared for manufacturing work at outlets of all sizes.
Collaborative robots are smaller and lighter than some industrial robotic arms, they usually embody sensors, software program, and different options to make them simpler to program and to work alongside individuals. Prior to now few years, they have become extra highly effective, extra exact, and even simpler to make use of, famous Common Robots.
The unit of North Studying, Mass.-based Teradyne Inc. demonstrated a number of cobot functions with choose companions throughout its open home. Every one mixed a UR arm with sensors similar to those from SICK, finish effectors from OnRobot and Schunk, and Common Robots’ personal controllers. In contrast to typical industrial robotic workcells, the displays didn’t require security cages.
Common Robots additionally provided displays all through the day, discussing subjects starting from a buyer use case and danger assessments to the way forward for work. Listed here are 5 takeaways from the occasion:
1. Collaborative robots are prepared for palletizing
Placing packing containers or instances on pallets may be strenuous, repetitive work. Bigger cobot arms, advances in movement management, and Common Robots’ concentrate on functions quite than know-how for its personal sake led to a veritable explosion of automated palletizing demos at this 12 months’s commerce exhibits, similar to Automate, ProMat, and PACK EXPO.
Robotiq confirmed its Robotiq Palletizer, which included a UR10 arm. Ryan Weaver, vp, industrial, mentioned how “lean robotics” greatest practices might help corporations get began with automation.
“We had talked loads about lean robotics earlier than the [COVID-19] pandemic, however now it’s time to assist corporations with adopting robots,” he informed The Robot Report.
On show was the UR20 mannequin, which is now delivery. It may deal with payloads of 20 kg (44 lb.), making it appropriate for palletizing, welding, and different duties as soon as the province of commercial robots.
Different Common Robots companions round palletizing included methods integrator Flex Line, with its boxEZ Field Erector.
Cell Industrial Robots, which can also be owned by Teradyne, confirmed its MiR 250 autonomous cellular robotic (AMR). Brian Dillman, gross sales director at Odense, Denmark-based Cell Industrial Robots, talked about how logistics can go “from good to nice utilizing AMRs.”
Many AMR customers have gone from “kicking the tires” to eager to scale their robotic fleets inside and throughout amenities, Dillman mentioned. He provided steering on the way to handle such rising fleets.
2. Cobots supply flexibility for machine tending
The best mixture of machine imaginative and prescient, software program, and UR cobots can facilitate CNC machine tending. Nonetheless, implementation generally is a problem, noticed Tyler Bouchard, co-founder and CEO of Flexxbotics.
Flexxbotics offers help for cobot machine tending, and the corporate claimed that its FlexxCORE software program connects robots with different tools for duties similar to deburring. With an edge field and cloud-based platform, it’s straightforward to use programming throughout cells, famous a Flexxbotics consultant on the open home.
Precision Cobotics, one other Common Robots associate, demonstrated its laser marker for selecting operations.
3. Common Robots continues to develop its ecosystem
“We initially anticipated solely 200 individuals,” mentioned Zach Tomkinson, regional supervisor for East U.S. gross sales at Common Robots.
Attendees got here from as far-off as Georgia and North Carolina for the one-day occasion. They included a mixture of potential finish customers, integrators, engineers, startups, and college students, in addition to organizations similar to MassRobotics. A number of informed The Robotic Report throughout networking that they had been in search of options to widespread business challenges.
Whereas Common Robots has specialised in collaborative robotic arms, it mentioned its rising UR+ partner ecosystem allows customers to seek out the correct mix of already-compatible applied sciences for his or her wants.
As an example, Kane Robotics displayed its GRIT-ST system for precision floor ending, and ESTIC America demonstrated an automatic nut runner for meeting. New Scale Robotics confirmed its Q-Span system with a UR cobot for automated gauging.
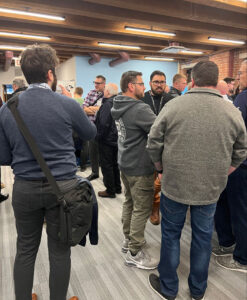
Greater than 400 individuals attended UR’s open home. Supply: Common Robots
4. Automation is turning into accessible to outlets of all sizes
Power-torque sensors present a way of contact, and rising integration of imaginative and prescient methods is permitting robots to maintain selecting autonomously quite than hand over after a single attempt, defined Andrew Pether, principal innovation analysis engineer at Common Robots.
Together with demonstration studying and streamlined consumer interfaces, outlets that don’t have robotics experience can now undertake automation, he mentioned.
Vermont Creamery defined the way it journeyed from “analysis to FAT” (manufacturing facility acceptance check) as a UR buyer. Rick Bart, director of operations; Chris Freeman, operations supervisor; and Eric Duncan, supervisor for environmental well being and security, supplied the end-user perspective on a profitable deployment.
Vectis Automation confirmed its Cobot Welding Instrument for fabrication outlets, and Cobot Programs displayed its Laser Welder. Hirebotics additionally affords built-in welding automation together with UR cobots.
Along with its open home, Common Robots hosted coaching classes at its headquarters as a part of its “UR Academy.”
5. Don’t concern robots and AI — they’re right here to assist
Regardless of widespread experiences warning of job losses on account of robotics adoption, such a correlation hasn’t been confirmed, mentioned Julie Shah. She is a professor on the Massachusetts Institute of Know-how’s Pc Science and Synthetic Intelligence Lab (MIT CSAIL).
“Our lab prefers to concentrate on ‘positive-sum automation’ quite than a ‘zero-sum’ stalemate,” she mentioned in a session on the way forward for work. Shah mentioned her analysis is engaged on computing at augments human functionality.
As well as, small and midsize companies characterize 48% of U.S. manufacturing and make use of 43% of producing employees, Shah added. If solely one-tenth of automotive suppliers are utilizing robots and all complain of a dearth of expert employees, automation is a part of the answer of upskilling labor, she mentioned.
Shah divided industrial automation into three phases. From 1962 to about 2010 was the “Don’t go there” stage, with heavy robots caged away from human employees.
2011 to 2021 was the “Get out of the best way” part, with cobots and collaborative cellular robots studying to maneuver or cease round individuals, in response to Shah.
On a associated subject, Chris Savoia, head of strategic enterprise growth at Common Robots, lined how and why to conduct danger assessments for cobots in a separate session. Collaborative robots are designed to be safer to function round people, however customers should nonetheless take workspaces, payloads, and processes into consideration, he mentioned. Happily, there are greatest practices and requirements to assist, Savoia mentioned.
From 2022 into the longer term could possibly be the period of “constructive sum automation,” mentioned Shah, as robotics builders overcome challenges similar to when a robotic freezes utterly in proximity to a human co-worker.
Gentle curtains, a spread of sensors and software program, and synthetic intelligence to foretell human movement can all assist robots grow to be extra conscious, she mentioned. Such predictive talents, together with extra correct simulation and measurement, can result in higher integration and check, Shah mentioned.
Whereas it’s nonetheless early days for generative AI and human-machine interplay, Shah mentioned the perfect productiveness outcomes are possible not from “lights-out,” totally automated factories however from smart collaboration between people and robots.
[ad_2]
Source link