[ad_1]
Hearken to this text |
Gearbox producer SEAT Componentes wanted to automate the unloading of 18,000 machined gears a day at its plant in Spain to ensure the standard of the elements. The corporate built-in 10 collaborative robots from Universal Robots utilizing solely inner assets.
This formulation made it doable for SEAT to maintain know-how on cobot configuration in-house, eliminating further programming and upkeep prices. The do-it-yourself set up was performed with out altering the present manufacturing unit format, permitting new purposes to be configured in lower than 1 hour.
Consequently, the company has diminished errors, improved employee security, and now has a crew ready to tackle new automation initiatives.
The enterprise problem
SEAT is a producer of gearboxes for the Volkswagen Group vegetation in Europe, Asia, and America. It provides them for a wide range of vehicles made by each Volkswagen, Audi, SEAT S.A., and Skoda.
At its plant in Barcelona, Spain, SEAT manufactures gearboxes, starting from the casting of the aluminum to the meeting of the housing, which incorporates gears, shafts, synchronizer, and the differential gearbox.
The corporate additionally performs the next high quality management. It’s a very specialised and complicated course of through which high quality and precision are crucial to ensure right operation and noise discount of the gearbox.
Unloading the elements and making them obtainable for the gearbox meeting course of was carried out fully by hand with operators unloading and transporting the elements on trolleys. A course of SEAT needed to automate to scale back errors and enhance security.
“The purpose is to make sure that from the machining course of to meeting, the operator touches the half as little as doable,” defined Fonseca, senior supervisor of technical providers at SEAT.
Cobots to the rescue
SEAT’s upkeep crew primarily based its automation method on expertise gained from an earlier mission from 2015 through which it put in UR cobots at its shotblasting and washing stations. The corporate realized that cobots had been simple to put in, keep, and combine without having security measures resembling fencing primarily based on carried out threat assessments.
Since utilizing cobots simplified and streamlined the shotblasting and washing course of, the crew really helpful integrating cobots once more to unload elements within the manufacture of gearboxes.
SEAT determined to combine 10 UR10e collaborative robots to hold out the unloading. The corporate may undertake that activity with out the providers of an exterior integrator due to its earlier expertise with the cobots. This assured price financial savings each on the time of set up and in future upkeep duties.
Performing the mixing of the UR cobots with SEAT’s assets concerned two levels of coaching and preparation. First, the SEAT Componentes Upkeep crew educated throughout the firm, beginning with the free UR Academy on-line coaching modules.
Second, the crew carried out a pilot mission through which it built-in an preliminary cobot.

Cobots supply small footprint and ease of use
Throughout this pilot take a look at, SEAT studied the prices and implementation intervals of a collaborative robotic, the protection necessities that the know-how required, and the technical feasibility of the operation.
The cobots handed the take a look at.
“We determined to make use of robots from Common Robots because of their simple programming and integration within the line, and above all due to their low footprint,” mentioned Francisco Pérez of the SEAT Componentes Upkeep Technical Workplace. “We had been in a position to set up them with out altering the present layouts, permitting the robots to work alongside the operator.
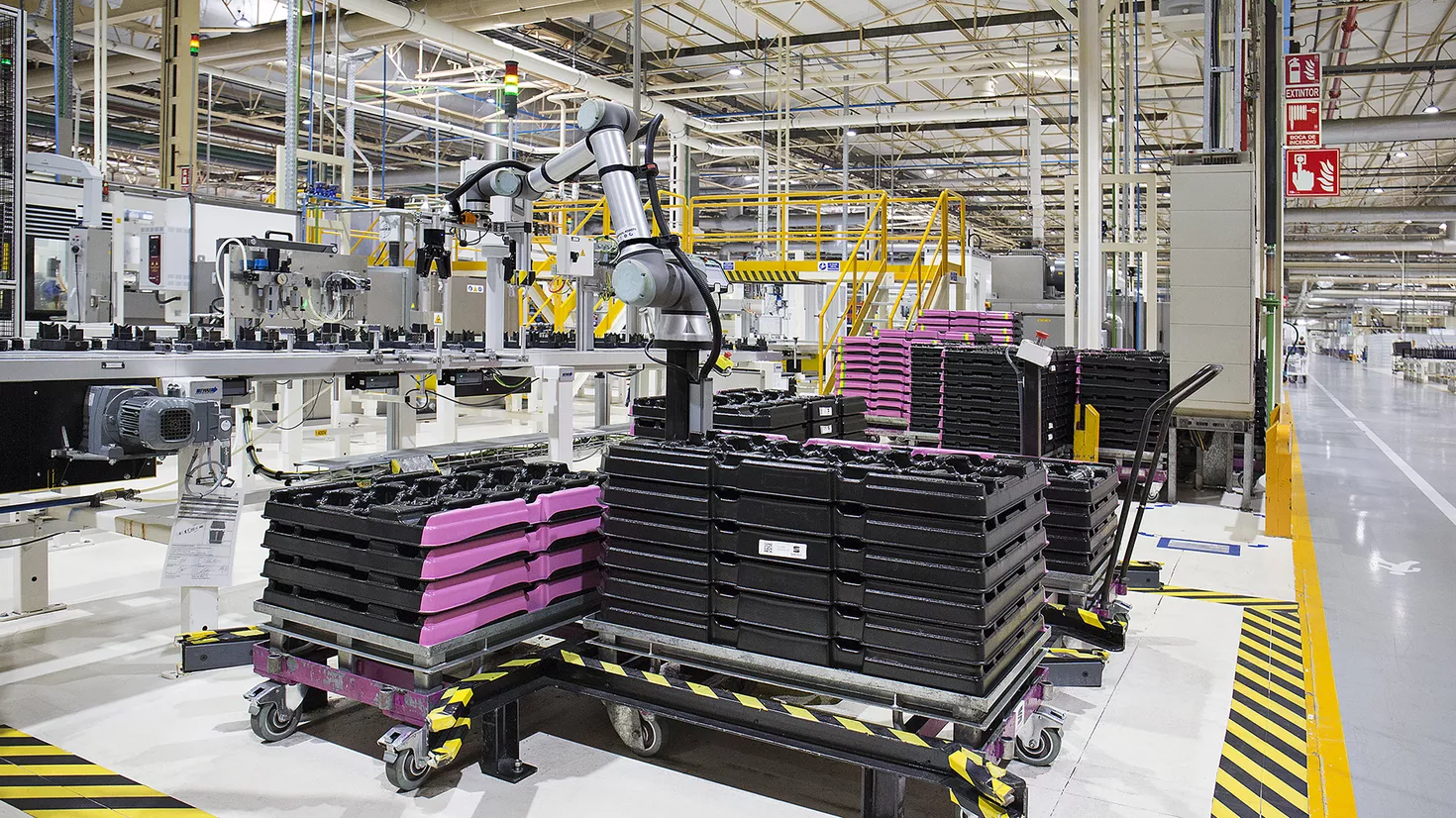
No fastened installations
The UR10e cobots presently serve 10 completely different machining traces. They don’t seem to be fastened installations, however they’ll simply be tailored to mannequin modifications.
“In lower than 10 minutes, we are able to adapt a cobot to switch from unloading one half to a very completely different part,” Francisco Pérez identified.
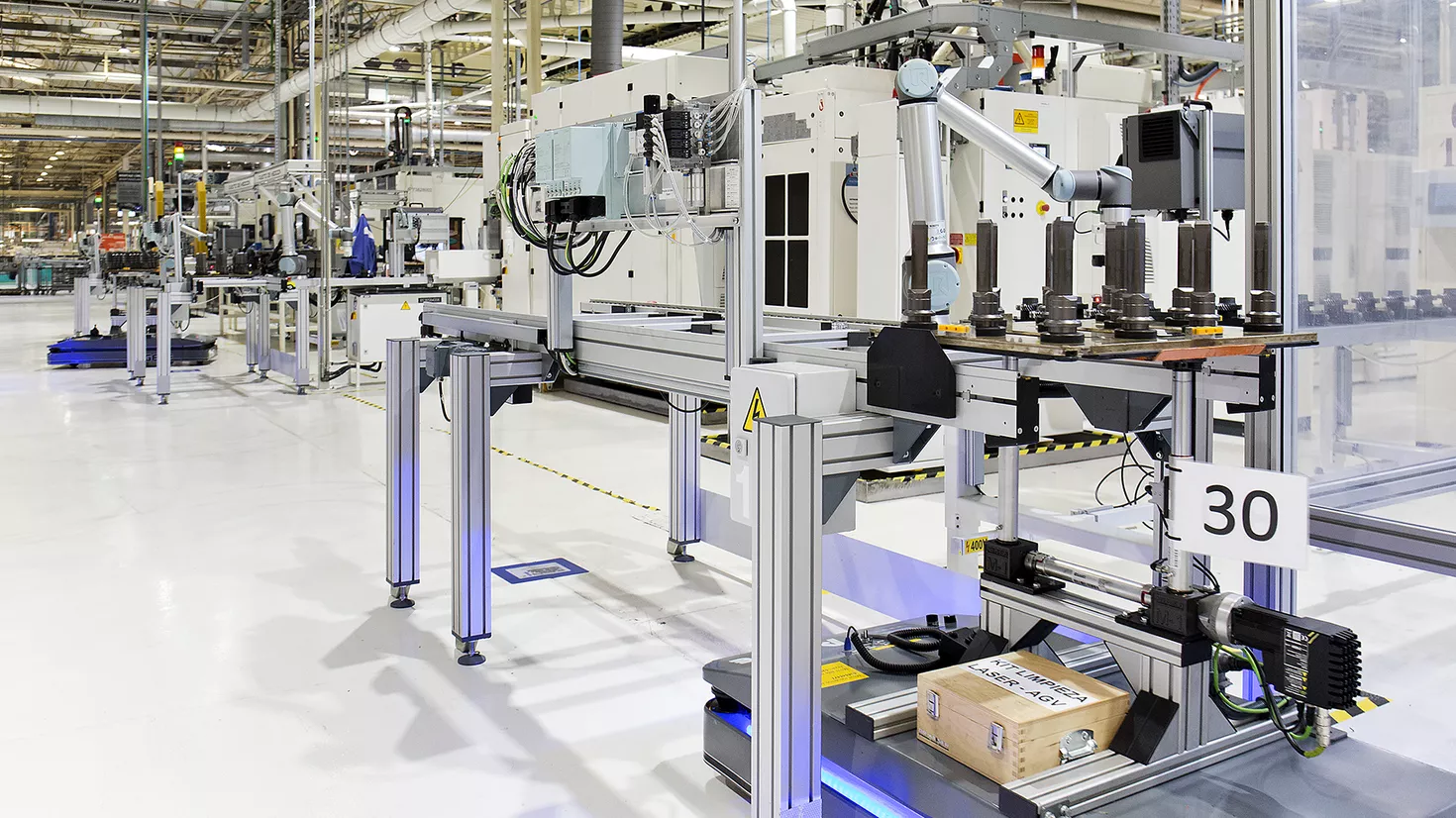
Elevated machine uptime
Utilizing the PROFINET protocol, the cobot communicates with the PLC and receives directions as to when there are already machined items in order that it could actually carry out the associated operation. When that’s the case, the cobot unloads the elements onto trays.
As soon as the tray is full, the PLC communicates with the autonomous cell robots (AMRs) to take away the total tray and insert a brand new one, thereby minimizing machine stoppages.

Simply-in-time manufacturing eliminates surplus inventory
The AMR transports the elements to a warehouse that’s stuffed simply in time in line with manufacturing wants, avoiding surplus inventory and the prices these entail. Having reached this level, all the pieces is now prepared for the gearbox meeting line: The gears are positioned on a particular meeting tray, and thru a sequence of automated operations, the remaining gearbox elements are connected.
Inside this synchronized course of, the cobot complies with SEAT’s cycle instances to attain the plant’s each day manufacturing objectives.

Cobot No. 11 used for testing and validation
A further eleventh UR10e has joined the cobot fleet on the SEAT plant. This robotic arm is meant for in-house coaching and is mounted on a cell platform to get near machines and work facilities.
The UR10e permits operators to familiarize themselves with programming collaborative robots. Moreover, it permits idea checks and validations of recent installations to be carried out earlier than their integration into the road.

3D printing of gripper fingers
One other key issue within the integration of UR cobots by SEAT is that the plant is self-sufficient in printing the “fingers” of the collaborative grippers, in line with every want and the extent of safety required to take care of the protection degree of the appliance.
This makes it doable to have nearly instant spares with out the necessity for inventory and to carry out idea checks in lower than 45 minutes, mentioned the company.
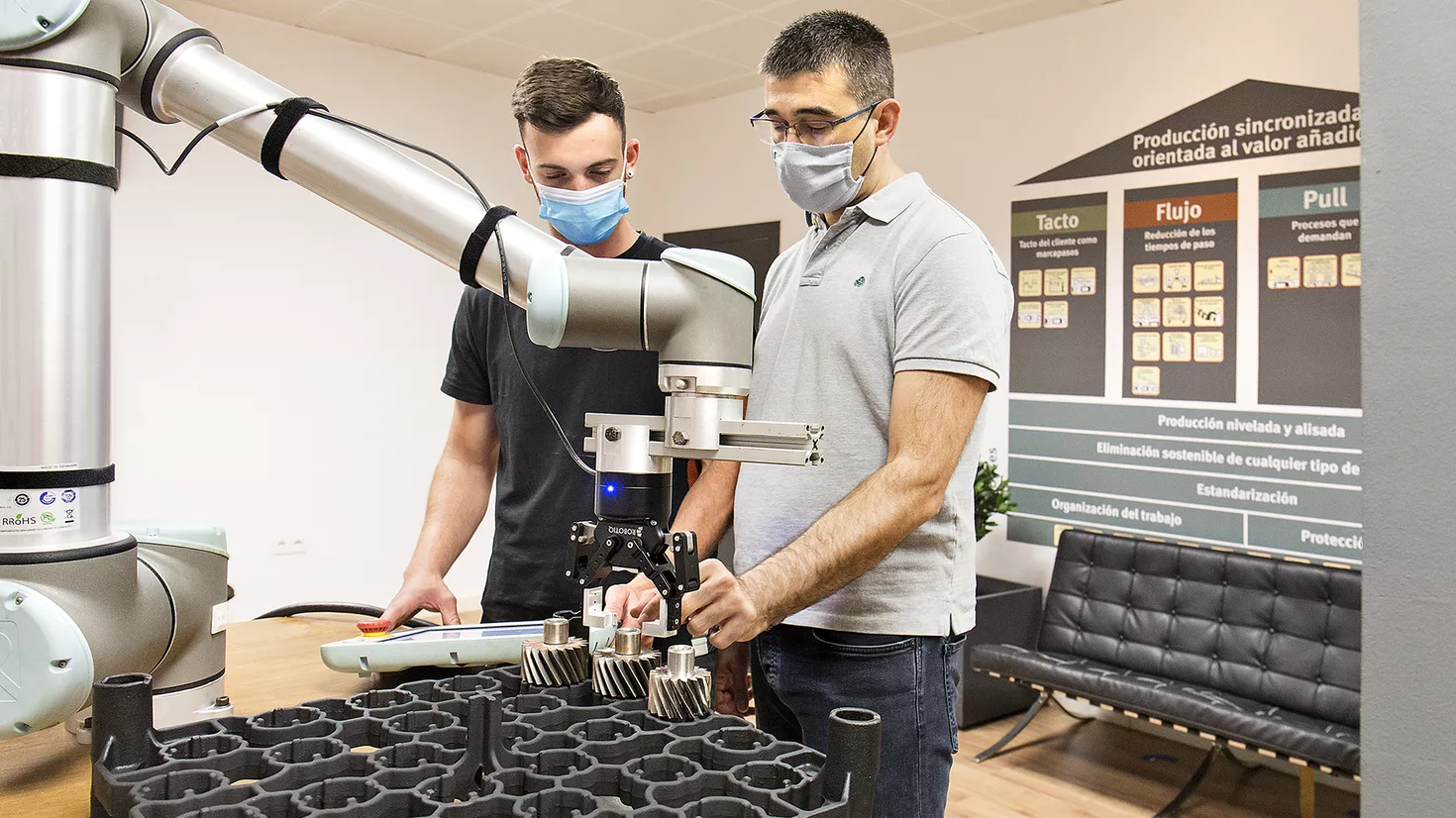
Data of cobots stored in-house
“Performing integration in-house has allowed us to maintain the know-how of programming and integrating the cobots throughout the upkeep space, which signifies that throughout any stoppages, we may be extra decisive and the prices of machine downtime are decrease,” mentioned Manuel Gómez, upkeep supervisor at SEAT Elements.
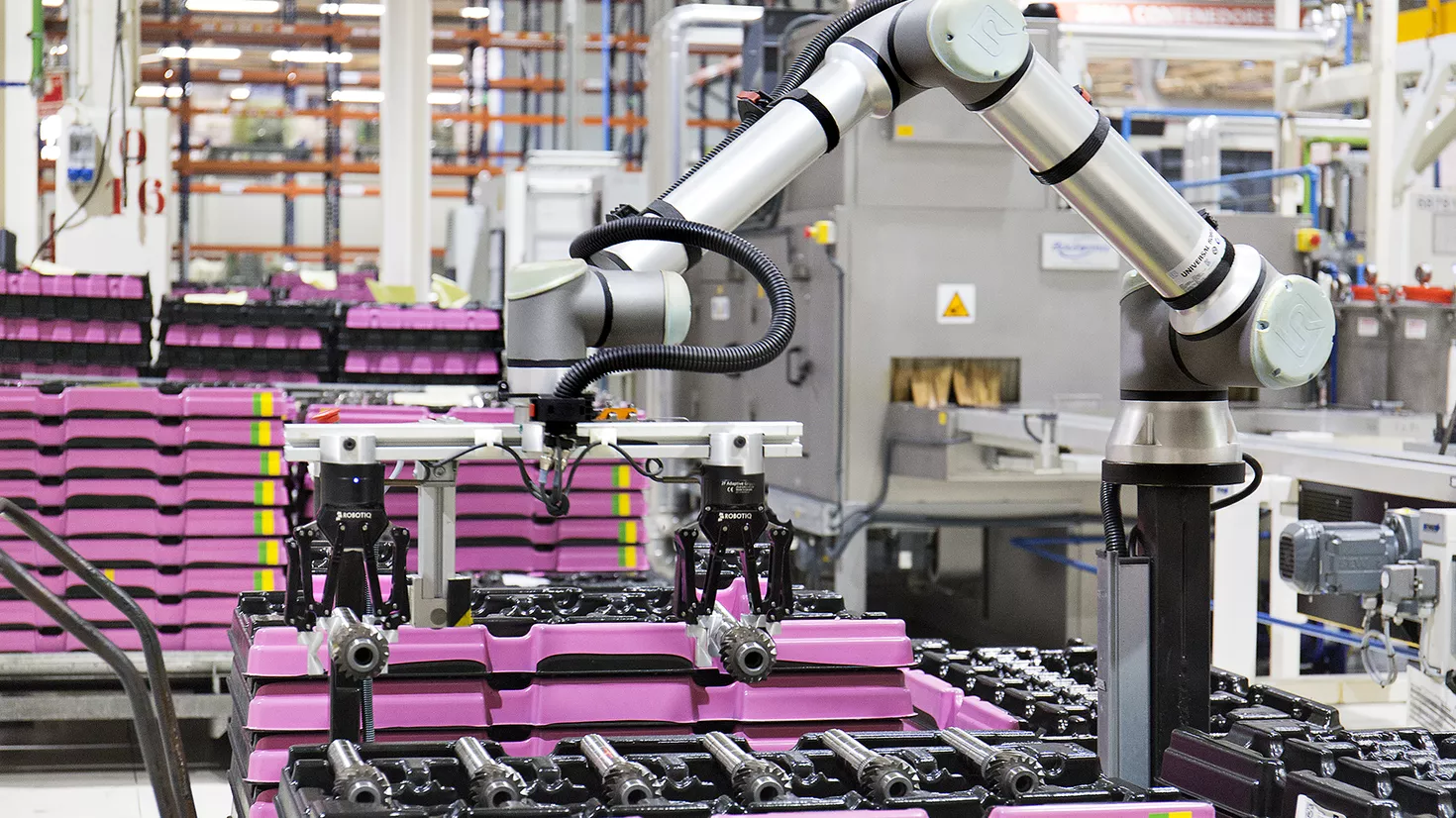
Intuitive gripper configuration
This ease when adapting to manufacturing was bolstered with the intuitive configuration of the cobots and their peripherals, licensed by the UR+ platform.
“We’ve got been in a position to implement purposes in lower than one hour,” Francisco Pérez emphasised. Furthermore, SEAT Elements can implement these modifications with out having to name upon the providers of an integrator, which might improve prices.
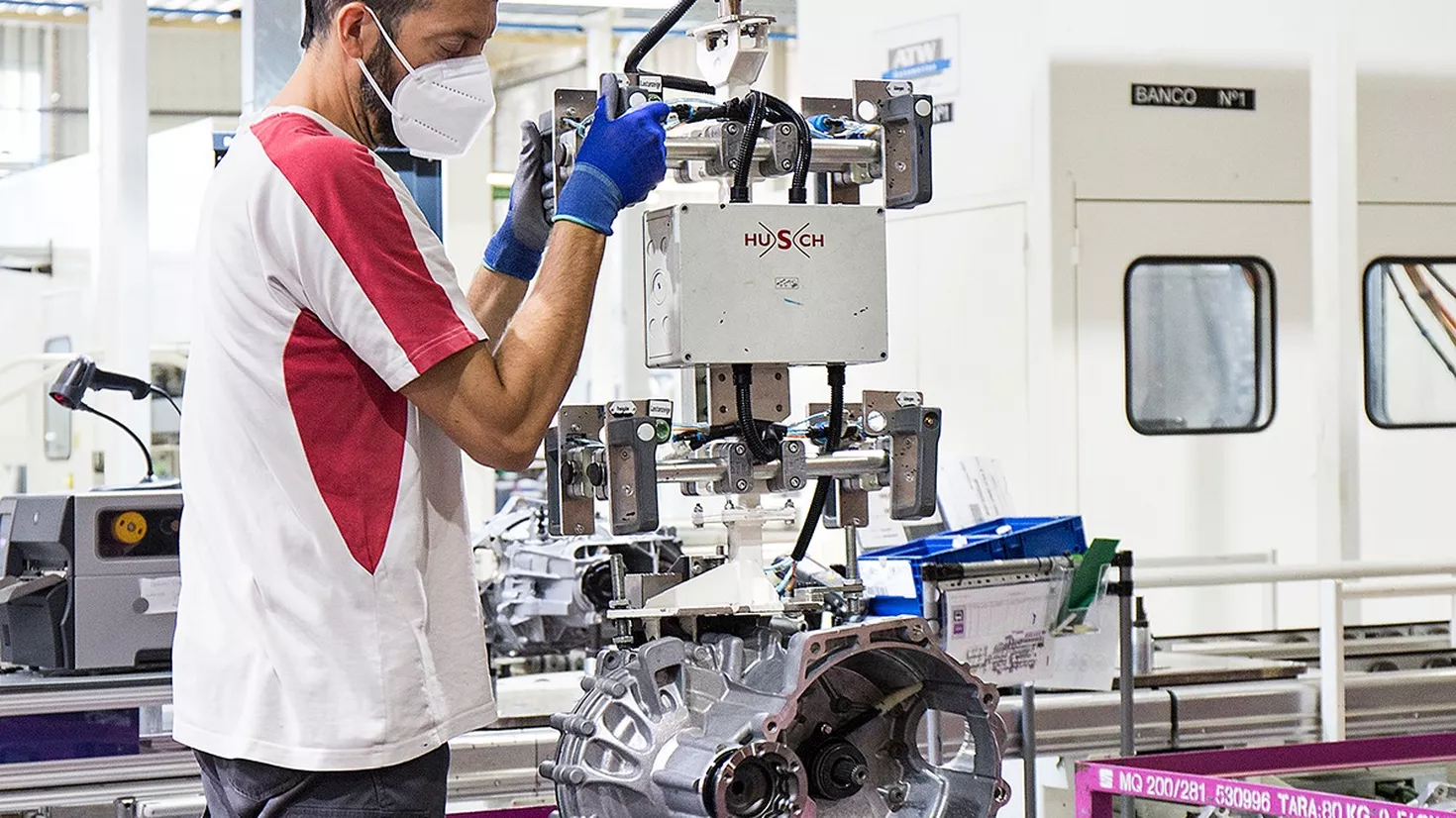
Cobots assist upskill operators
One other advantage of the appliance is that the operators have been relieved of manually unloading 18,000 elements a day.
“By utilizing collaborative robots, we’ve got managed to make sure that operators can commit their time to duties that add worth to the product, resembling high quality points or course of enhancements,” famous Gómez. He added because of this “the operators see the cobots as an additional instrument to do their work.”
All in all, SEAT has modified its perspective, permitting its crew members to tackle future automation initiatives in-house.
“Now, any automation mission is conditioned not solely by its contribution when it comes to profitability, but in addition as a result of it gives us with know-how that we didn’t have earlier than,” Gómez mentioned.
To sum up, the mission “is worthwhile, productiveness is larger, and high quality has been consolidated,” concluded Eduardo Fonseca. He mentioned the automation mission has gotten the approval of the SEAT group.
Editor’s notice: This text was syndicated with permission from Common Robots’ blog.
[ad_2]
Source link