[ad_1]
Hearken to this text |
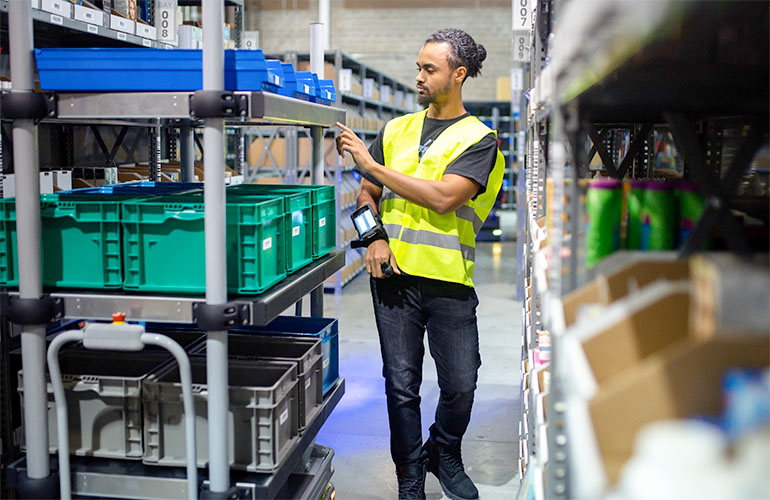
The Pyxis resolution from IAM Robotics is a whole person-to-goods workflow automation resolution. | Credit score: IAM Robotics
I lately reported on IAM Robotics launching an automatic resolution designed for person-to-goods (P2G) warehouse workflow. The corporate is getting into a brand new chapter targeted on the most well liked section of autonomous cell robotic (AMR) functions and one which has already been confirmed via the efforts of corporations like Locus Robotics and 6 River Systems.
The rebirth of IAM Robotics is important as a result of it’s the newest chapter in what was a valiant try and commercialize cell manipulators. It’s additionally a poignant lesson in failed market match and figuring out when to pivot as a robotics startup.
A basic storage startup
IAM Robotics began in Vlad Altman’s Pittsburgh basement and shortly moved to an area township storage constructing to mannequin a working warehouse. Co-founder Tom Galuzzo had a ardour for cell robots and a robotics diploma from Carnegie Mellon College. On the time, the concept of placing a robotic arm onto a cell platform and utilizing it to select objects from cabinets was one of many remaining “holy grail” challenges in robotics.
It was additionally a 12 months after Amazon’s historic acquisition of Kiva Systems for $775 million – the potential for robotics in warehousing was within the highlight. It took till 2015 for IAM Robotics to lift its first seed spherical and introduce its Swift robotic on the promise of automated selecting within the warehouse.
This was when IAM Robotics first appeared on my radar as an revolutionary resolution for goods-to-person workflows within the warehouse. On the time, I used to be main product administration for the cell robotic enterprise at Adept Know-how, and no different vendor available in the market was commercializing a cell manipulator for warehousing functions.
The corporate was pushing the boundaries of robotics expertise, concurrently fixing the issues of vision-guided cell manipulation and creating methods for AMR notion, impediment avoidance, and the challenges of battery-supported operations.
Utilizing cell manipulators to select from cabinets
What instantly struck me in regards to the Swift robotic was that it didn’t decide up particular person objects from bulk SKU bins saved within the warehouse. Somewhat, it labored by selecting from inventory that was saved in organized rows on a shelf, not not like what you would possibly see within the front-of-house retail area of your nook drugstore.

The unique IAM Robotics Swift cell manipulator autonomously picked objects from neatly organized warehouse cabinets. | Credit score: IAM Robotics (Wayback Machine Archive)
I had by no means seen a warehouse area with merchandise organized in neat product rows like this, and that was my first pink flag in regards to the viability of Swift. To make the system work, Swift required a 3D mannequin of every product SKU. With the 3D mannequin, the robotic’s imaginative and prescient system might then establish the merchandise on the shelf and decide the proper pose of the robotic to accumulate the merchandise.
The corporate developed a novel 3D merchandise scanning station known as “Flash” that may ingest a brand new product SKU, picture it and add it to the 3D library of things that Swift might now deal with.

IAM Robotics initially developed a whole resolution that included a 3D scanner, enterprise software program and a warehouse selecting robotic. | Credit score: IAM Robotics (Wayback Machine Archive)
To operate correctly, Swift additionally needed to autonomously deal with product replenishment, placing objects onto the warehouse cabinets in these neat and arranged rows. The thought to replenish the cabinets autonomously regarded nice on an ROI spreadsheet, however Swift wasn’t quick sufficient (in comparison with human warehouse associates) at replenishing the cabinets in the actual world. It additionally couldn’t simply work side-by-side with human associates in warehouse aisles resulting from its working dimensions.
One other concern for the viability of Swift was the goal section of “warehouses with extremely organized cabinets” was simply too small. Nearly all of warehouses and distribution facilities retailer bulk objects contained in bins or packing containers on the warehouse cabinets. Bulk storage is solely probably the most environment friendly and cost-effective methodology of utilizing treasured warehouse area.
Lastly, the lack of Swift to select objects from bins (the “holy grail” utility) in the end sealed its destiny. Within the warehouse, people are very adept at pulling particular person objects from bulk storage. This realization led the corporate to rethink its portfolio.
Creation of an AMR platform
Quick ahead to 2020, and IAM Robotics made the primary pivot with the design and launch of its Bolt AMR, utilizing the entire information and expertise gained from engineering Swift. The aim of Bolt was to supply a normal AMR base that may very well be deployed into any AMR utility. This was a aggressive market with numerous established distributors, together with corporations like OMRON, Fetch Robotics, MiR, OTTO Motors and others.
Sadly, this was additionally the beginning of the pandemic. Whereas e-commerce was exploding in reputation (together with the demand for automated assist for warehouse labor shortages), there have been additionally a whole bunch of AMR rivals available on the market with customary AMR platforms. The novel innovation for Bolt was a swappable battery that may very well be shortly modified with minimal downtime of the AMR. Nevertheless it wasn’t sufficient.
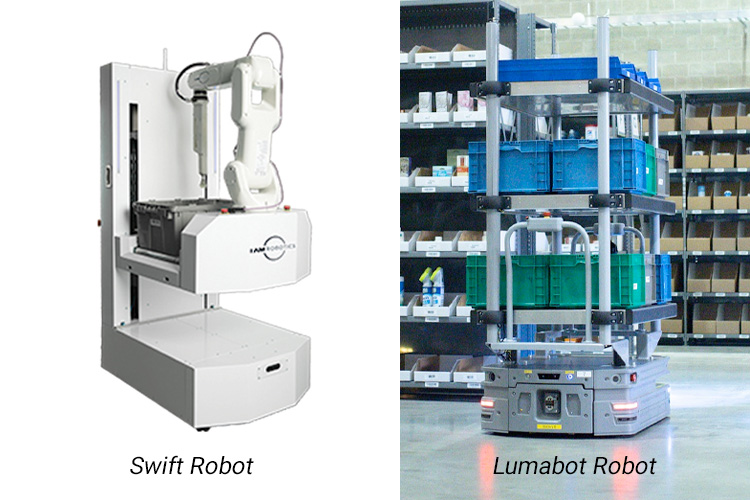
IAM Robotics developed two AMRs, the G2P Swift (left) and new P2G Lumabot (proper). | Credit score: IAM Robotics
In 2021, the corporate restructured, employed CEO Lance Vandenbrook, let go of most of the authentic cell manipulation-focused engineering groups, employed the required enterprise software program engineering workforce and entered a self-imposed “stealth mode” to retool.
Particular person-to-goods workflow is the new utility section
The corporate lately re-emerged with a brand new person-to-goods (P2G) warehouse workflow, leveraging the entire mental property from its early days in AMR growth and including a brand new, sturdy, totally featured enterprise workflow layer on prime.
The brand new Pyxis (pronounced pix-us) resolution is designed to be aggressive with current P2G options reminiscent of Locus Robotics and 6 River Techniques. The main focus for IAM Robotics has modified from being a cell robotics firm to a warehouse workflow firm, managing the duties of each human associates and cell robots.

The brand new Lumabot is designed particularly for person-to-goods automation in a warehouse. | Credit score: IAM Robotics
The corporate launched a brand new AMR known as Lumabot, taking the Bolt AMR base and outfitting it with a payload of fastened cabinets and decide/put-to-light guides. Human associates interface with the answer via a wearable that communicates buyer orders, amount and SKU areas.
Lumabot robots transfer autonomously to the decide location the place people pull particular person objects from bins and place them in outgoing buyer order bins. The Lumabots then take assembled buyer orders to pack out stations for ultimate consolidation, packaging and labeling.
The Pyxis resolution manages the operations of the entire human associates within the warehouse, along with the fleet of Lumabots to handle buyer order selecting and consolidation. The system is designed to be deployed in both greenfield or brownfield alternatives and supplied as a robots-as-a-service (RaaS) business model.

The Pyxis resolution directs the human associates with details about which merchandise to select and the place to position the merchandise for a buyer order. The Lumabot then strikes objects to a pack-out station. | Credit score: IAM Robotics
[ad_2]
Source link