[ad_1]
Hearken to this text |
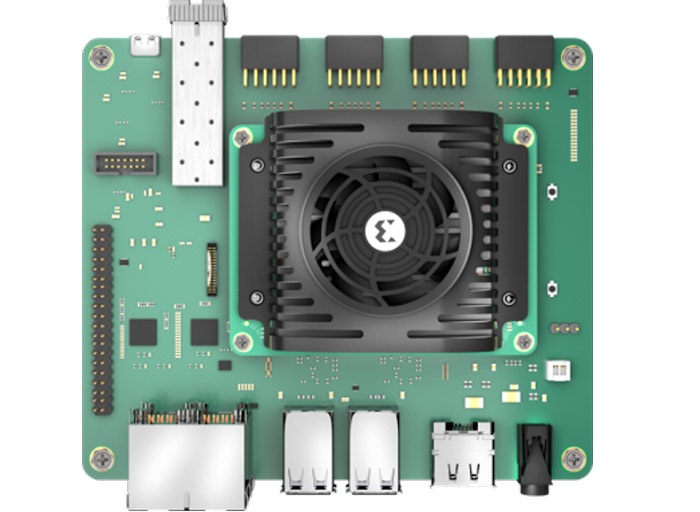
Robotics competitors groups can use the Kria KR260 Robotics Starter Equipment. Supply: AMD
From college students and startups to the world of leisure, curiosity in robots is all over the place lately. In visiting with roboticists of all kinds throughout the globe, Superior Micro Gadgets discovered that profitable robotics design typically comes down to 3 key issues: Timing is every part, the entire is larger than the sum of its components, and distribution beats centralization.
Timing is every part in robotics
Simply as location is every part in actual property, timing is every part in automation. Should you’ve ever been on a video name, they’re usually achieved utilizing a “best-effort” Web connection.
You will have even skilled a brief state of affairs the place audio and video fall out of sync with one another. It is because the info connections we’re all so accustomed to, whether or not or not it’s a hardwired Ethernet connection, Wi-Fi, or cellular, usually are not the identical as these used on this planet of robotic automation.
Automation calls for synchronization above all else. Synchronization is the results of determinism in communications and motion. In different phrases, it’s when the brains of the robotic inform its arm to maneuver a bit of sheet steel to a selected place or a number of robots work collectively on a joint job comparable to rotating and spray portray a bit of sheet steel.
Issues ought to occur after they’re presupposed to, with out fail. This dance happens with millisecond-level precision as a result of, on this planet of automation, time is cash.
If determinism is half of the timing equation, latency is the opposite half. Latency lets you go quick as a result of latency pertains to the period of time it takes for one thing to occur. Latency refers back to the time of sensor enter from a digicam or gyroscope to the time it takes to react to the info the sensors share.
More and more, robots are getting used round folks in collaborative conditions. People are infamously unpredictable, and impediment avoidance is an instance the place time from sensor enter to response makes a important distinction.
Timing requires each determinism and low latency, and when you have each, it’s typically generically known as being “actual time.” Quickly cultivating the chain of occasions from sensor inputs to information processing to mechanical motion has vital worth in business, because the temporal worth of information can slip by you want a fish in water in the event you aren’t fast sufficient to react to it.
Nobody is aware of this higher than Robert Huber, co-founder of Radmantis. The aquaculture startup is growing a system that makes use of imaginative and prescient AI to grade salmon as they swim and a collection of underwater mechanical gates to type comparable fish collectively earlier than cargo to eating places, based mostly on weight, well being and different elements.
“Salmon can get wired simply and stress ranges are mirrored within the high quality of the top product,” stated Huber. “Utilizing real-time imaginative and prescient AI together with real-time controls, the fish are unassuming individuals in guaranteeing restaurant orders are fulfilled to spec and on the highest high quality.”
Construct issues better than the sum of their components
Many roboticists discovered their begin with FIRST — For Inspiration and Recognition of Science & Know-how — a nonprofit providing hands-on, STEM applications for over half 1,000,000 college students in over 90 international locations. FIRST college students rapidly study the idea of the entire needing to be better than the sum of the components, and so they study it in additional methods than one.
“To maximise productiveness, we break up the crew into 4 targeted teams,” recalled Alex Van Aacken, a former FIRST Robotics Competitors participant and present mechanical engineering pupil at Ohio State College.
“We had a design sub-team, a prototyping and manufacturing sub-team, an meeting sub-team, and a testing sub-team,” he stated. “The robotic itself additionally wanted to be divided up into the bottom chassis, the robotic arm, and the body connecting the robotic arm to the bottom chassis.”
Van Aacken was fast to notice that the event software program his crew used additionally wanted to help this modularized method.
Robots might be among the many most complicated of techniques, in order that they should be break up up into a number of subsystems with a number of groups engaged on these particular person subsystems and yet one more crew assembling the techniques collectively to do the meant job. Similar to an orchestra is made up of particular person musicians and a conductor organizes them to play collectively, the mixing step is important in engaging in the ultimate robotic end result.
Distribution beats centralization
In some robots, the subsystem has some stage of autonomy by offloading processing from the principle controller. The advantage of this distribution of processing is usually each simplicity and efficiency.
For instance, a primary robotic controller could inform a robotic arm subsystem to do a job however not do the duty. If the arm has the liberty and functionality to do stated job extra effectively as a result of it has entry to data that the principle controller could not have, it’s thought-about an instance of decentralization of controls. illustration is from the hit worldwide TV present, BattleBots.
Parker Holloway and Greg Needel are members of Group Switchback, featured within the final two seasons of the present. They defined the advantages of the principle articulating arm on their robotic being an offloaded management subsystem separate from the principle controller to do speedy and impartial calculations comparable to matrix multiplications.
“All of that matrix multiplication permits us to do movement profiling in order that we all know that we’re all the time exerting the utmost torque of the arm that’s secure for the trajectory that it’s on,” stated Holloway.
“The principle controller simply has to specify the place it desires the arm to be, and the subsystem takes care of transferring the arm to that location as quick as it could possibly go given the place and situation the arm was in,” Needel added.
In distinction, a centralized setting could require fewer digital parts. That method could carry a decrease preliminary bill-of-materials, but it surely typically sacrifices high quality with substantial wire harnessing resulting in a single level of failure that may solely be solved by changing an costly centralized module or debugging a labyrinth of wiring connections.
An additional advantage, modularity permits the developer to finish frequent asynchronous know-how refreshes of particular person subsystems versus much less frequent and extra complicated, full top-to-bottom redesign within the centralized case.
The issues which are true in robotics improvement are sometimes true in on a regular basis life. Curiosity in robotics is yearly setting new data amongst youth. Creating robotics is instructing them the significance of being well timed and reliable, teamwork, and breaking apart issues into items and assembling these chunks right into a completed resolution.
Robotics can also be instructing younger innovators to diversify and empower each bit of the system to deal with its duties. This may translate to all elements of society, irrespective of in the event that they proceed their pursuit of robotics improvement or not.
In regards to the writer
Chetan Khona is the senior director of business, imaginative and prescient, healthcare, and sciences at Superior Micro Gadgets Inc. (AMD). Captivated by the artistic potential of embedded gadgets to unravel embedded design challenges in a basically differentiated and environment friendly method whereas a pupil on the Georgia Institute of Know-how, Khona has been concerned within the embedded gadgets business for greater than 30 years.
AMD is a sponsor of the MassRobotics Form and Function Challenge, whose winners can be introduced on the Robotics Summit & Expo in Could in Boston.
[ad_2]
Source link